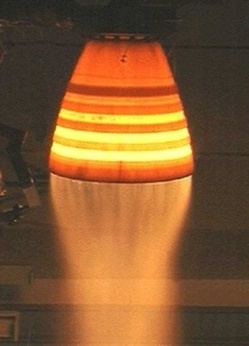
Actuellement en phase de test sur une pièce de moteur CFM56, les matériaux composites thermostructuraux, très résistants aux hautes températures, ouvrent des perspectives nouvelles aux motoristes et aux avionneurs. Une technologie que Safran maîtrise déjà pour la propulsion militaire et spatiale.
Herakles (Safran) réalisait il y a un an une première dans le monde de l’aéronautique civile en testant un moteur équipé d’un cône d’éjection des gaz en composites à matrice céramique (CMC), appartenant à la famille des composites thermostructuraux. Capables de résister à des températures allant de 1 000 à 1 500 °C, les CMC sont particulièrement adaptés pour ce type de pièces très exposées à la chaleur des moteurs. Ils devraient aussi permettre des gains de masse de l’ordre de 30 à 50 % par rapport aux pièces métalliques actuellement en service qu’ils ont vocation à remplacer.
« Jusqu’ici, nous avions seulement utilisé ce type de matériaux thermostructuraux pour des appareils militaires, explique Yann Richard, chef de programme « Echappement CMC » chez Herakles. Comme toute technologie de rupture, celle-ci nécessite une vision à très long terme. Nous avons commencé à explorer la piste de l’aéronautique civile afin de pouvoir produire en série des pièces qui pourraient équiper la prochaine génération de moteurs LEAP, ainsi que les nouveaux moteurs que développera Safran à l’horizon 2020-2030. »
Contrairement au domaine militaire, où le nombre d’heures de vol des appareils est plus limité, les moteurs d’avions civils sont extrêmement sollicités. En plus d’une forte résistance aux très hautes températures, les pièces doivent pouvoir afficher une durée de vie de plusieurs dizaines d’années.
« Pour les moteurs militaires, nous utilisons des matériaux thermostructuraux à base de fibres de carbone. Ils ont cependant tendance à s’oxyder au cours du temps. Afin de répondre aux attentes du secteur de l’aéronautique civile, nous utilisons une fibre inoxydable en carbure de silicium, explique Yann Richard. Nous avons également ajouté à ces matériaux une nouvelle spécificité : l’autoréparation. Si des microfissures se forment dans la pièce, l’oxygène présent dans l’air va activer des molécules permettant à la pièce de s’auto-cicatriser en temps réel. Cette propriété est essentielle pour atteindre les 100 000 heures de fonctionnement requises par une pièce de moteur civil. »
D’ici quatre à six mois, Herakles devrait obtenir la certification de l’EASA (« European Aviation Safety Agency ») afin de tester le cône d’éjection sur des vols commerciaux, en partenariat avec Air France. « La compagnie aérienne s’est montrée très intéressée par ces nouveaux matériaux et suit de près l’avancée de notre programme, précise Yann Richard. Ce partenariat est également très positif en termes d’image pour Safran. »
Herakles (Safran) réalisait il y a un an une première dans le monde de l’aéronautique civile en testant un moteur équipé d’un cône d’éjection des gaz en composites à matrice céramique (CMC), appartenant à la famille des composites thermostructuraux. Capables de résister à des températures allant de 1 000 à 1 500 °C, les CMC sont particulièrement adaptés pour ce type de pièces très exposées à la chaleur des moteurs. Ils devraient aussi permettre des gains de masse de l’ordre de 30 à 50 % par rapport aux pièces métalliques actuellement en service qu’ils ont vocation à remplacer.
« Jusqu’ici, nous avions seulement utilisé ce type de matériaux thermostructuraux pour des appareils militaires, explique Yann Richard, chef de programme « Echappement CMC » chez Herakles. Comme toute technologie de rupture, celle-ci nécessite une vision à très long terme. Nous avons commencé à explorer la piste de l’aéronautique civile afin de pouvoir produire en série des pièces qui pourraient équiper la prochaine génération de moteurs LEAP, ainsi que les nouveaux moteurs que développera Safran à l’horizon 2020-2030. »
Contrairement au domaine militaire, où le nombre d’heures de vol des appareils est plus limité, les moteurs d’avions civils sont extrêmement sollicités. En plus d’une forte résistance aux très hautes températures, les pièces doivent pouvoir afficher une durée de vie de plusieurs dizaines d’années.
« Pour les moteurs militaires, nous utilisons des matériaux thermostructuraux à base de fibres de carbone. Ils ont cependant tendance à s’oxyder au cours du temps. Afin de répondre aux attentes du secteur de l’aéronautique civile, nous utilisons une fibre inoxydable en carbure de silicium, explique Yann Richard. Nous avons également ajouté à ces matériaux une nouvelle spécificité : l’autoréparation. Si des microfissures se forment dans la pièce, l’oxygène présent dans l’air va activer des molécules permettant à la pièce de s’auto-cicatriser en temps réel. Cette propriété est essentielle pour atteindre les 100 000 heures de fonctionnement requises par une pièce de moteur civil. »
D’ici quatre à six mois, Herakles devrait obtenir la certification de l’EASA (« European Aviation Safety Agency ») afin de tester le cône d’éjection sur des vols commerciaux, en partenariat avec Air France. « La compagnie aérienne s’est montrée très intéressée par ces nouveaux matériaux et suit de près l’avancée de notre programme, précise Yann Richard. Ce partenariat est également très positif en termes d’image pour Safran. »